BWTS 3D Laser scanning services
- este es el autor
- 8 dic 2020
- 1 Min. de lectura
Actualizado: 15 ene 2021
In earlier times, a design engineer on board uses tapes to measure and records the measurements of the existing systems, spaces available. These recorded measurements are then used in developing engineering documents.
As the earlier method requires a lot of time and errors may occur in measurements, an alternate solution for this is 3D laser scanning as it requires less manpower which takes multiple scans in an hour. A 3D Laser Scanning plays an important role which helps to take decisions to Design Engineers for the installation of BWTS.
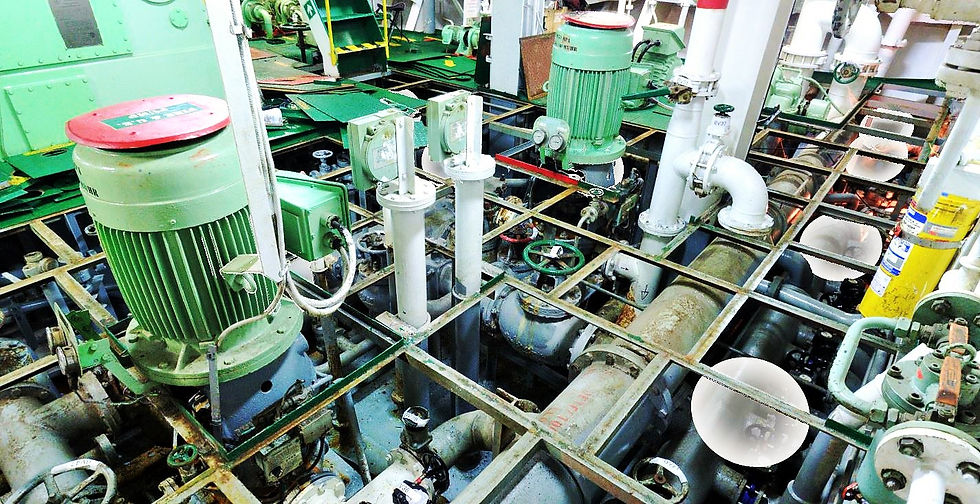
Scanning can be done when the vessel is in operation/or at anchorage/or during the port call. Scanning provides precise measurements and high detail of existing piping and structure. All required areas like ballast piping, Engine room & Pump room are scanned with a 3D laser scanner to install BWTS. Scans are taken from various locations to cover the equipment. These scan data can be compared with the design to verify that all components are installed in the correct locations. If any errors are noted, the design will be revised. These scan data can be used for various purposes like BWTS & Scrubber installation, Clash detection, damages to the ship structure, and Air Ducts.

The new BWTS with its piping system can be seamlessly planned and integrated with the scan data. These scan data are used to find out the clashes with the vessel’s existing system and the modification that is needed for the installation of BWTS. To decide how and where to install a BWTS on the vessel, a feasibility study or pre-survey has been conducted.
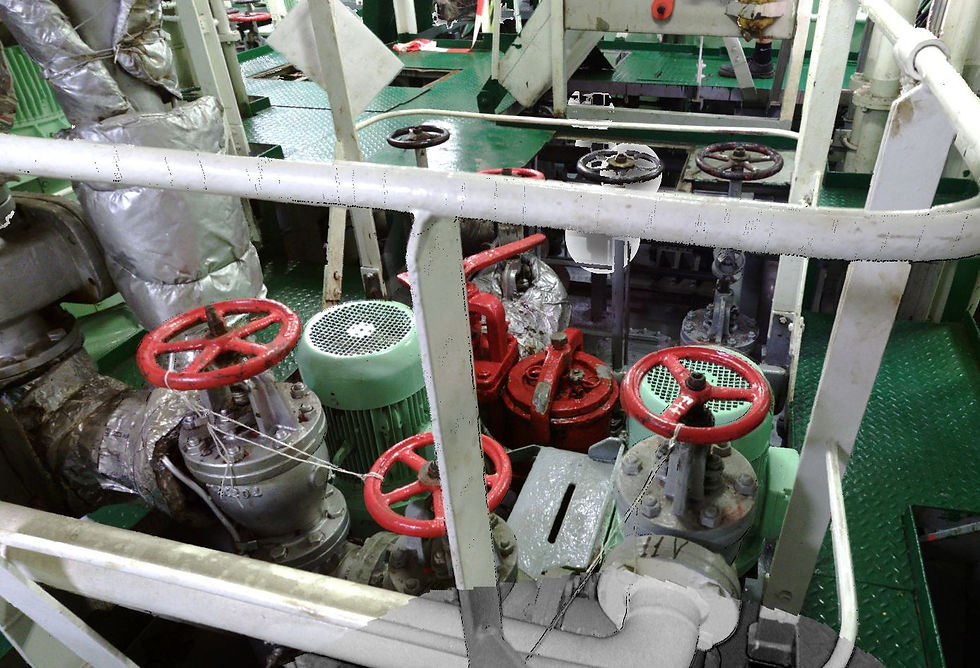
Comments